Baseline
Energy Management
In order to track performance and demonstrate improvements, you have to know where you started from. Defining an Energy Baseline is the foundation for benchmarking performance and measuring improvements over time. The ideal baseline is to determine a ‘normal year’ for the facility from an energy consumption perspective (e.g., not abnormally high or low) by which changes can be measured from. The objective of a proper baseline is to provide a ‘control’ by which to distinguish efficiency and performance gains from other influences such as weather, production mix and output, and other variables affecting significant energy uses.
Data Hierarchy and Quality
There are several data collection methodologies for energy metrics including:
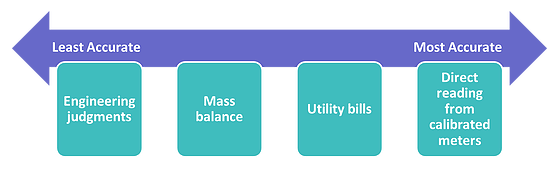
With different methodologies, come varying levels of accuracy. Sites must collect data using reasonably available methods that produce the most accurate results using available resources. The preferred source of primary data is directly from utility meters or through other direct measurements, such as sub or temporary meters. Engineering judgment and estimates should not be considered an acceptable long-term methodology for data collection.
Maintaining or improving data quality is an important consideration. Data collection methods for each data element should be documented and include a description of the measurement technique and the margin of error, if applicable (e.g., meter calibrated in accordance with manufacturer specification designed to be accurate ±10 percent). While following manufacturer specifications for calibrating and maintaining meters is recommended, best practice is to calibrate meters at least annually to ensure acceptable data integrity.
Energy Baseline Adjustments
Adjustments to the baseline year data may become necessary under certain scenarios to ensure that comparisons are consistent. The following scenarios or cumulative combination of one or more scenarios are examples of situations that may necessitate energy baseline adjustment:
- Mergers, acquisitions, and divestments
- Insourcing or outsourcing activities if those activities were not included in the base year
- Changes in calculation methodologies or improvements in emissions factors/activity data
- Errors or omissions of metrics data from the base year
- Equipment or process changes, including expanded production and/or changes in major energy consuming equipment
- Energy source changes (e.g., change source fuels, installing a CHP system)
In all cases, the baseline year data should only be adjusted if any one change or combination of changes alters the base year data by greater than the threshold of five (5) percent.*
*Based on significance threshold from The Climate Registry’s General Reporting Protocol; http://www.theclimateregistry.org/resources/protocols/general-reporting-protocol/
This threshold may be applied at the site/category, business unit/sector, divisional, or corporate levels as needed to ensure comparability of data at various levels of the enterprise.
For mergers, acquisitions, or divestments, a baseline year data adjustment should only be conducted if the site in question existed during the base year. If a site did not exist until after the base year, the energy baseline does not need readjustment. In the case of a structural change that occurs in the middle of a given year, the base year data should be updated for the entire year to avoid necessary recalculations the following year.
Addressing Material Errors, Omissions, and Variations
As with any management or performance program, data integrity and accuracy is an important consideration. Addressing material errors, omissions, and variations in a timely manner will ensure that time and effort are properly focused on the greatest opportunities and that ongoing performance is being accurately measured and reported.
Material Errors – discovery of material errors (i.e., greater than five (5) percent variance from the total reported metric) in a reported metric are important to address in a timely manner and corrected within the data collection system. This applies to the current reporting year and previous reporting years back to and including the baseline year. It is best practice to document an explanation of corrected data, including identifying the root cause, defining and communicating necessary controls, and preventing the error from arising in the future.
Data Omissions – data found to be omitted from a reported metric, and has greater than a five (5) percent variance from the total reported metric, are also important to address in a timely manner and corrected within the data collection system. This applies to the current reporting year and previous reporting years back to and including the baseline year. As with material issues, it is best practice to document corrections, identify root causes, and implement proper controls to prevent future omissions.
Data Variations – large variations in data can be an indication of a potential error and result in missed opportunities and misinterpretation of performance. For example, if a metric varies by more than five (5) percent from the same period in the previous year this could be a valid variation, or it could be an indication that the data element may be in error. It is important to evaluate and track variations. If larger variations are believed to be accurate a reasonable explanation for the variation should be documented or ‘flagged’ to minimize unnecessary reviews on the recurring variations. As a measure of good practice, regular comparison of invoiced quantity with metered or measured quantities should be completed. Overall, one should not expect a variance of more than 2-3%.
Estimating Missing Data
A meter malfunction, catastrophic events, and a variety of other factors can result in the loss of data. In the event this occurs, best practice is to estimate the data and document the methodology used to perform the estimate (e.g., assumptions, calculations, known vs. estimated data). Although there is no one correct way to estimate data, the best practical methodology should be used which yields a reasonable result, can be documented and allows for reporting with full transparency.
The following are common and widely accepted data estimation methods:
- Engineering estimates
- Obtaining backup data in the form of utility invoices, purchase records, or back-up metering
- Normalizing prior months’ or years’ data on a per unit basis, and using that information combined with production output for the missing period to estimate the information
- Using regression analysis for one or more metrics over an extended time period where data is available to estimate the missing information
- Using generally accepted estimation techniques (e.g., online calculators or industry-specific default values)
Individuals reporting estimated data should document why the data is missing, the approach used to estimate (e.g., engineering estimate, normalization on a per unit basis), and any underlying assumptions made. From a data integrity perspective, estimates are not preferred or recommended as an acceptable long-term methodology for data collection.
Create an Energy Baseline for Consistent Benchmarking