Metering
Energy Management
When it comes to energy, the saying “you can’t manage what you don’t measure” is especially applicable. The continuous measurement, monitoring and collection of energy data is what informs and supports continued improvement of energy management and drives Key Performance Indicators (KPIs), Benchmarking, and Goal & Target Development.
Unfortunately, most utility bills do not include enough granularity or frequency of data to understand where usage is occurring and inform timely decision-making. Energy metering, whether simple or advanced, allows your organization to ‘take control’ of real time consumption and the relationship to production demands. Such control allows greater ability to identify, explore (e.g., evaluate spikes or trends), and act on energy efficiency opportunities.
Classification of Metering Infrastructure
BIER recommends using the standard terminology to define the hierarchy of a production plant and classify the appropriate metering infrastructure. According to this standard, an organization is broken down into 6 levels:
- Enterprise – A grouping of production sites within the same corporate structure
- Site – A physical production plant producing a homogenous suite of goods
- Area – A logical group of production cells that work together to produce a product(s) (Packaging, Liquid production, Utilities)
- Process Cells – represent a logical grouping of equipment that includes the equipment required for the production of one or more batches. Individual lines within a department (brewing, fermentation, Can line, boiler house)
- Unit – a collection of process equipment that carries out major processing activities
- Equipment – a functional group of equipment that can carry out a finite number of specific processing activities, (pasteurizer, kettle, boiler)
ISA-88: A standard addressing batch process control and a design philosophy for describing equipment and procedures.
In operations with a moderate to low level of complexity, it can be appropriate to simplify the structure by removing levels of hierarchy such as the ‘Unit’. For the purposes of this guidance, we will refer to production plants as having 4 levels: Site, Area, Process Cells, and Equipment.
Energy Metering Minimum Requirements
Before exploring optimal metering infrastructure and tools for converting metered data to useful information, it is important to point out a couple of considerations with regards to minimal metering requirements:
Accounting and Regulatory Reporting Requirements – depending upon the jurisdiction, there may be metering requirements related to energy and GHG emissions regulations and reporting. Such requirements, by and large, are limited to total site metering of purchased fuel, heat, cooling and electricity. One exception to this is mandatory GHG reporting that requires monitoring of process emissions and/or metering of energy or industrial gases at the sub-site level. For guidance on treatment of process emissions in the beverage industry, please refer to the BIER GHG Emissions Sector Guidance.
Utility ‘Fiscal’ Meters – many facilities rely upon meters maintained by the utility provider which relate to total site fiscal metering (meters used to determine the consumption charged for energy purchases). It is not uncommon for these meters to periodically give inaccurate readings.
Best Practice: A production site is advised to have Company-owned meters to validate the fiscal meter readings to protect against over-billing.
Optimal Metering Infrastructure
Defining the optimal metering infrastructure for an organization or site will depend upon numerous criteria, the scope boundaries, and resource availability. Energy metering and tracking accomplishes different objectives at different levels within a production site. For example, Area-level metering and tracking is largely for the purpose of monitoring performance against energy use KPI and holding departments accountable for managing energy resources. Process cell and Equipment-level monitoring of metered data is likely to be more frequent (e.g. daily or weekly) as its primary objective is to identify problems and over-consumption through short-interval-control (SIC).
The following provides common criteria for determining the optimal metering infrastructure for a site:
- Regulatory requirements for reporting energy use or GHG emissions;
- The materiality of the cost associated with the particular energy consumption;
- The capital cost and maintenance costs of meters to monitor a given energy use;
- The need to create energy cost centers and/or monitor energy costs by brand/SKU;
- The potential for using metered data to optimize energy consumption of a given process or equipment;
- The energy management maturity of Managers, Supervisors, and Operators; and
- The manufacturing systems infrastructure of the site and the ability to automate the capture and storage of meter readings.
Best practice is to develop and document a metering and tracking standard which is applied to all production sites of a similar nature. “Planning Investment in Metering Infrastructure” provides greater detail on the contents of a metering and tracking standard.
Optimal infrastructure for a non-energy intensive production site – On one end of the spectrum a production site can be characterized as having moderate-to-low energy costs, no need for batch or SKU assignment of energy costs, and/or a low maturity in energy management. The optimal metering infrastructure for such a site would likely be Site and Area-level metering of electricity and heat which would be used to set KPI and drive accountability for energy use. Best practice for non-energy intensive sites is to track energy performance by department at least on a weekly basis and aligned with production meetings.
Non-energy intensive sites are still likely to have a few pieces of equipment (e.g. HVAC, lighting and compressed air) that are large sources of consumption and are responsible for 70 to 80% of total site use. Given the significant proportion of energy use by this equipment, measurement of energy consumption on a frequent basis (i.e., daily) is highly recommended. A general rule of thumb is to limit the scope of what is considered a ‘significant source or consumption’ to equipment which contributes over 20% of a given utility out of the area total. This is just a general guideline with the actual threshold determined by each organization on the basis of the specific concentration of energy use.
Optimal infrastructure for an energy intensive production site – On the opposite side of the spectrum, energy intensive production sites are those characterized as being significantly exposed to energy price volatility, requiring more advanced tools for assigning costs to batches or SKU’s, and/or having an average to high level of energy management maturity. The metering infrastructure at such sites commonly extend to capture energy use from all major process cells and to all equipment that represents a significant source of consumption. Consumption data is often captured using automated systems that incorporate production context and provide outputs to help visualize consumption. Best practice at energy intensive production sites involves tracking and monitoring consumption at Equipment and Process Cell levels on at least daily basis.
The definition and threshold for what constitutes a ‘Significant Source of Consumption’ is commonly lower than for non-energy intensive sites.
Planning Investment in Metering Infrastructure
Regardless of whether the sites in an organization are characterized as energy intensive or not, the approach to planning new metering infrastructure and tracking tools follows the same logic:
- Prioritize driving accountability for energy use
- Define a Metering and Tracking standard for your organization
- Establish a 3-year plan for incremental investments
- Prove you can use the data to inform decisions before investing in significant metering infrastructure
Energy Metering and Tracking Standard

Prioritize driving accountability for energy use
Holding the users of energy accountable for their consumption requires providing them with sufficient information to track and accurately measure their performance. Accountability for energy performance throughout the organization needs to be the driving force that leads to greater investment in metering and tracking infrastructure and tools. This will ensure that metered data is put to good use to inform decision-making, as meters alone will not result in energy efficiency or conservation.
“Measurement is the first step that leads to control and eventually to improvement. If you can’t measure something, you can’t understand it. If you can’t understand it, you can’t control it. If you can’t control it, you can’t improve it.” Dr. H. James Harrington
Executing a metering plan without implementing the appropriate accountability for energy performance will invariably lead to large amounts of data that is not used to inform decisions and is at most used to explain poor performance after the fact.
Driving accountability for energy performance within an organization is best driven from the top-down and using the structure provided by a Management, Control, and Reporting System (MCRS). At a minimum, the best practices used by BIER members is to set energy reduction targets at Area level and have the metering, tracking, and processes in place to hold Area Managers accountable for performance against defined targets.
This accountability will lead to more informed decisions about the appropriateness and scope of further investment in metering infrastructure and tracking tools to set targets and monitor performance at Process Cell and Equipment levels.
Define a Metering and Tracking Standard for your organization
A metering and tracking standard that is integrated into a continuous improvement program will ensure that all production sites consistently meet the minimum standard and will provide the synergies and cost savings associated with standard processes. Best practice is to include, at a minimum, the following elements in a metering and tracking standard:
- Requirements for minimum metering of Area-level energy consumption.
- Requirements for sites to develop and execute calibration plans that meet standards for measurement accuracy and calibration method and frequency, as well as processes for error identification. “Measurement Accuracy” describes measurement accuracy in more detail.
- Definitions of KPIs for energy management and MCRS processes for tracking results as well as correcting poor performance. This includes the frequency with which KPIs and other performance indicators are monitored.
- Guidance on use of calculations and estimations to monitor energy consumption where measurement using meters may not be appropriate or possible.
- Guidance on the use of performance indicators (PI) for short-interval-control of significant sources of energy consumption.
- A meter map or data sheet containing information on meter locations, types of meters, system name, data parameters, units of measurement, manufacturer and last calibration date. This information should be easily accessible and reviewed at least annually to ensure changes, additions, and modifications have been documented.
- A defined process for evaluating gaps in metering infrastructure and planning to fill these gaps.
Establish a 3-year plan for incremental investments
BIER recommends that each production site complete a metering gap analysis. This first involves defining a meter map that outlines the utility meters that exist at Site, Area, Process Cell and Equipment levels in a way that is consistent with the organizational structure and scope of KPIs. The mapping of meters to the organizational structure of the facility will allow for the identification of gaps in the ability to accurately generate PI’s and KPI’s at all levels within the Site.
The metering gap analysis will allow for a prioritization of investment in metering over the organization’s longer-term planning horizon. It will also aid in the correct positioning of meters so that they align with KPI by reflecting the same organizational boundaries or cost centers.
When conducting a metering gap analysis and/or developing a metering map, it is important to consider more than just the number and placement of meters. A site or organization’s metering infrastructure and approach will mature over time based upon need, energy management maturity, and resource availability. Figure 2 provides a maturity spectrum for energy metering with best practice being real-time monitoring with integration with production and business management, which allows for instantaneous monitoring and management of energy across the facility.
Figure 2. Metering: Indicators of Program Maturity
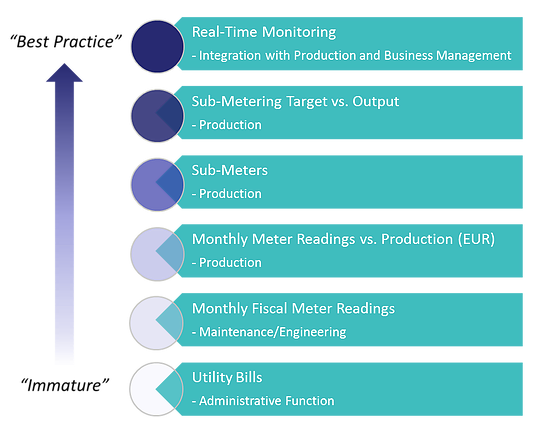
Prove you can use the data to inform decisions before investing in significant metering infrastructure.
Before investing in widespread energy metering infrastructure at Process Cell and Equipment levels, production sites should first demonstrate that Area-level metering is maintained and the data used to generate performance metrics that are tracked on a systematic basis. Area-level tracking of energy performance may be done using Excel but a more formal Energy Management Information System (EMIS) with automated data capture is highly recommended before investing significantly in metering at lower levels.
An EMIS will provide the analytics and reporting functionality that converts the consumption data into easily manipulated information that can drive better decision-making. Equally important, an EMIS with a user-friendly interface will go a long way in supporting accountability and ownership of energy performance by production line employees. In the absence of an EMIS, excel-based tracking will often lead to energy performance being the exclusive domain and responsibility of one or two individuals responsible for utilities.
EMIS Dashboard
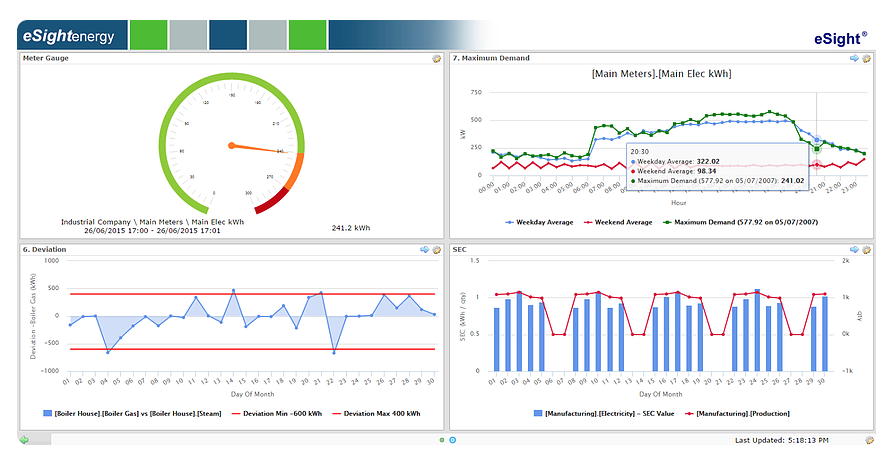
Measurement Accuracy
The metering infrastructure of a site is best maintained using a calibration plan that specifies the method, frequency and acceptable accuracy of all the meters on-site. Calibration can be resource-intensive and costly so the parameters of the plan must take into account the materiality of each source of consumption in deciding on the method and frequency of calibration, BIER recommends the following guidelines for meter accuracy:
Fiscal Meters – maintain systematic error at a level below 1%. Calibration should be done by certified instrumentation experts on a frequency determined either by regulation or by the manufacturer’s specifications.
Area-level Meters – maintain systematic error at a level below 2% for area-level meters providing the underlying data for KPI’s. Calibration would preferably be done on a frequency determined by the meter manufacturer’s specifications.
Process Cell Meters – maintain systematic error at a level below 3%. The calibration plan should include a process for data verification of individual meters that allows plant personnel to identify abrupt changes to the data or gradual drifts by comparing against budgets or benchmarks. The requirement to calibrate metering at this level could be triggered by the identification of a systematic error or meter failure using this process.
General Guidelines and Best Practices for Metering of Energy Resources
- Aligning metering of energy resource consumption with an energy management plan.
- Metering efficiently provides revealing data to support targeting continuing improvements and establishing the next energy efficiency targets.
- All meters are calibrated on a schedule directed from the manufacturer of the equipment.
- A back-up strategy for interpolating lost data is recommended.
Significant sources of energy use drive the granularity of metering data collection. Instrumentation and meters should be considered for all key energy users in the facility, power distribution centers and support system to monitor energy consumption, flow, pressure, and temperature (Steam, Air Chilled water, etc).
General Guidelines and Best Practices for Data Collection Intervals
- Aligning data collection interval capabilities with the energy management plan scope (electronic automatic or manual reading).
- Defining proper granularity of data collection intervals reveals energy consumption events that may otherwise be buried in a less granular collection program.
- Example: If measuring a significant source of steam use is a beverage pasteurizer within a packaging hall, a data collection of 30-60 seconds may be required to detect line stop events.
- Significant sources of energy use drive the granularity of data collection.
- Manually read data is converted to electronic form in a timely manner for graphing and comparison purposes.
- Data is properly backed-up on a regular schedule.
Energy Metering is the data collection that drives KPIs, Benchmarking, and Goal & Target Development